Introduction of French fries production line
Frozen French fries are made from potatoes through several processes: peeling, cutting, frying, degreasing, freezing, and packaging.
The advantage of quick-frozen fries is that they are convenient, fast, easy to preserve, and efficient, eliminating the need to run to the farmers' market, reducing the hard work of cleaning, peeling, and cutting potatoes, and satisfying the majority of customers.
The French fries production line is used for batch production of frozen French fries, which consists of corresponding machines.
Frozen French fries production line process flow:
Capacity: 200kg/h,400kg/h,600kg/h,800kg/h,1000kg/h,1500kg/h
Main products of Frozen French fries production line
Cleaning Elevator
The inlet of the elevator is about 40 centimeters above the ground, so the potatoes can be easily poured into the hopper by hand and lifted to the following process evenly and continuously.
It can reduce workers' labor intensity and constantly work in cocoa, which is convenient and practical.
Potato cleaning and peeling machine
The potato cleaning and peeling machine adopt the advanced brush principle to clean and peel the skin of potatoes.
The spiral blade propels the cleaning and peeling compartment, and the line operation can realize automatic continuous cleaning and peeling.
It is more convenient to use with the production line.Potato picking machine
While the potato picking machine is transported to the following process by mesh belt drive, the residual or incomplete peeled materials are picked by hand.
Workers can keep the workshop floor clean and tidy by throwing the picked scrap directly into the trash can.
The potato picking machine can work continuously and is easy to pick.
French fries machine
The potato cutting machine cuts out smooth and flat fries without breakage, good molding, high output, and smooth surface without roughness.
We can adjust the thickness of potato chips.
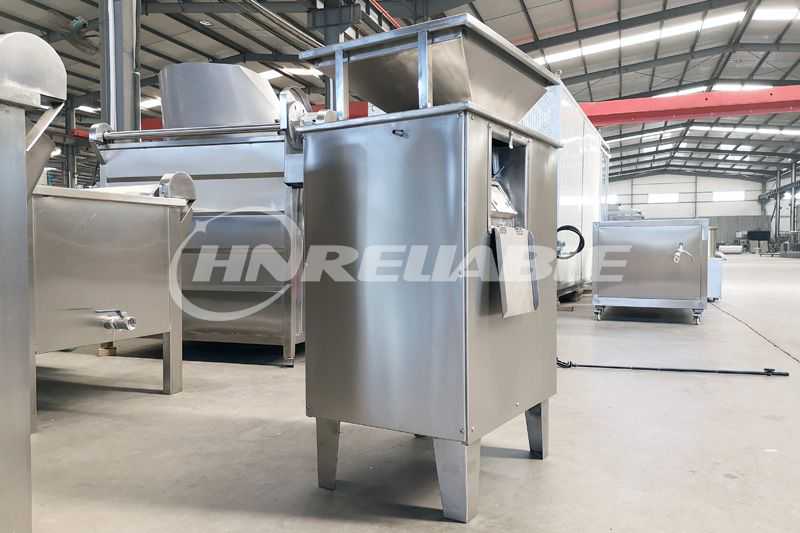
French fries cleaning machine
The conveyor conveys the potato strips to the potato strip washing machine.
The French fries washing machine is equipped with a bubble-generating device, which makes the potato strips tumble and effectively removes the impurities on the
surface of the potato strips, such as floating materials that can be overflowed from the overflow tank.
The sediment is discharged from the sewage outlet to achieve the purpose of cleaning.
The potato fries washing machine has the characteristics of thorough cleaning, energy saving, water saving, stable and reliable equipment, etc.
French fries blanching machine
French fries blanching machine plays the role of color protection.
The temperature is automatically controlled and set at will.
The heat source can be gas, electric, and other ways (according to the user's requirements).
Color protection at the same time can add food additives to ensure that the color of the fries is bright and good taste.
The fries blanching machine body uses food-grade stainless steel materials to meet food hygiene standards.
French fries cooling machine
The French fries cooling machine adopts the up-and-down tumbling of bubbles to imitate manual repeated scrubbing, which can quickly bring down the surface temperature of French fries.
The French fries cooling machine can effectively prevent the potato fries from over-bleaching and break up the material thoroughly, which is conducive to the uniformity of the frying, and finally conveyed through the mesh belt into the following process for further processing.
French fries air drying machine
The fries are conveyed through the mesh belt and turned over several times to realize the multi-side wind and uniformity of the fries.
The high-pressure wind of the fan cools the fries and dries the surface moisture.
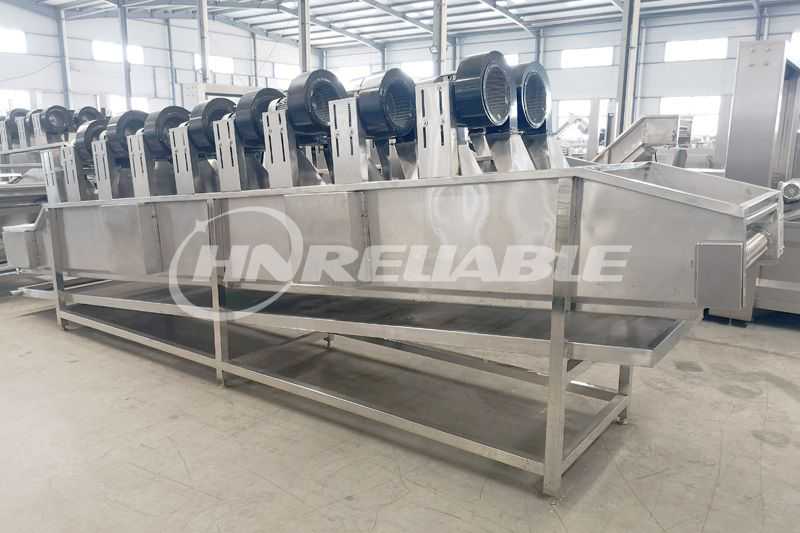
The winding nozzle is in the shape of a wind knife, which effectively improves the wind pressure and makes the water of the fries blow away or evaporate quickly, effectively preventing the phenomenon of oil popping when frying and shortening the frying time.
Vibrating screen
The vibrating screen is made of stainless steel, which is specially used to screen the waste or substandard size of fries and can further remove the moisture from the surface of fries.
The vibrating screen has an inclined angle, which can smoothly transfer the qualified fries to the following process, and is equipped with a collection port and tray to collect the screened scraps, which is very convenient to use.
French fries frying machine
The French fries frying machine is made of stainless steel, solid and durable, with free temperature control.
French fries frying machine adopts electric heating, and the thermal efficiency reaches more than 95%, saving energy.
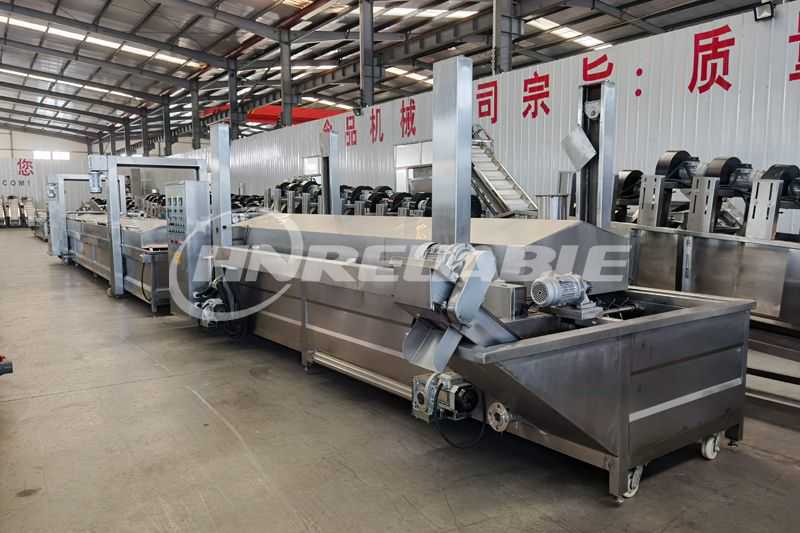
The oil has no charcoal and is equipped with an automatic oil filter to remove slag.
The oil will not turn black.
The use cycle is long, the color of the fried French fries is bright, and the product grade is instantly improved.
French fries de-oiling machine
After frying, the fries are transported through the mesh belt and quickly cooled and blown off the oil on the surface by the high-pressure wind of the fan.
The wind nozzle becomes a wind knife, effectively improving the wind pressure and making the fries' oil blow off quickly.
The French fries degreasing machine is equipped with an oil-catching tray. The blown oil can be collected and reused through the tray, saving oil and making the French fries not greasy and better in taste and convenient for storage.
French fries freezing machine
The French fries entering the French fries freezing machine are all fine products. The freezing machine can freeze the center temperature of French fries to -18° within a short period and quickly pass through the ice crystal production belt (0 to -5° range) within 30 minutes to reduce the loss of nutrients and original taste.
Automatic French fries packaging machine
An automatic French fries packaging machine can automatically complete the process of feeding, bag making, filling, bag making, date printing, counting, and finishing product output.
The automatic French fries packaging machine saves a lot of workforce and material resources, significantly save production costs, and has high reliability, intelligence, and excellent performance. Suitable for assembly line operation.